The Evolution and Importance of Rapid Prototyping Plastic in Business
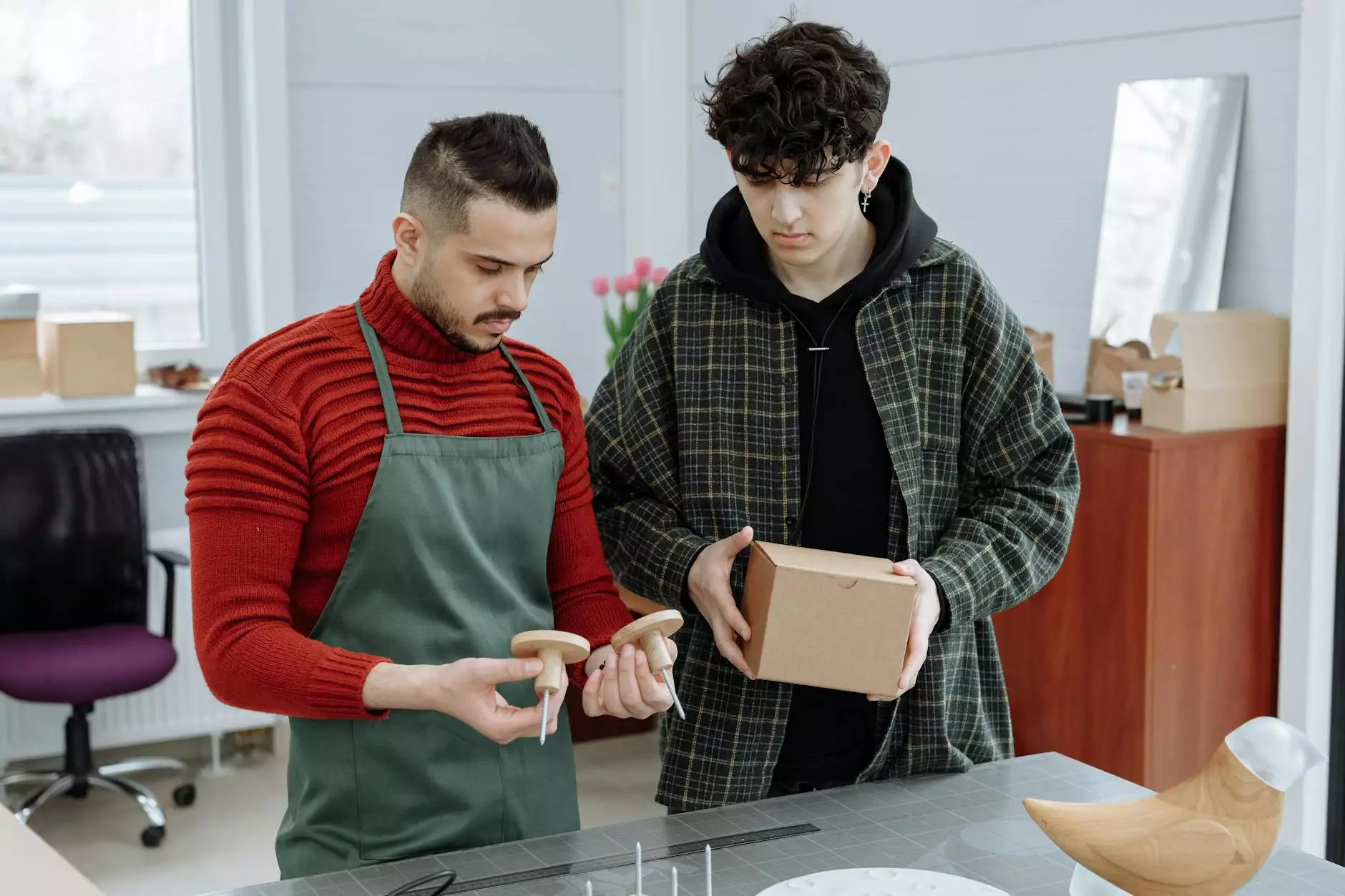
The business landscape has undergone a profound transformation in recent years, largely due to advancements in technology and innovation. One such advancement that has significantly impacted various industries is rapid prototyping plastic. This method of product development has become integral to businesses, particularly in the area of metal fabrication where precision, efficiency, and adaptability are paramount. In this article, we will explore the various facets of rapid prototyping plastic, its implications for businesses, and the future it holds.
What is Rapid Prototyping Plastic?
Rapid prototyping plastic refers to the use of various plastic materials in the rapid prototyping process, which allows designers and engineers to quickly turn their ideas into tangible products or components. The primary goal of this technique is to reduce the time and cost associated with traditional manufacturing processes while increasing design flexibility. By utilizing advanced technologies such as 3D printing, CNC machining, and injection molding, rapid prototyping enables businesses to test and validate their designs efficiently.
Benefits of Rapid Prototyping Plastic
Understanding the benefits of implementing rapid prototyping plastic within your business model can be a game changer. Here are some key advantages:
- Speed: Rapid prototyping allows for faster production of prototypes compared to traditional methods. This speed is critical in today's fast-paced market where time-to-market can determine the success of a product.
- Cost-Effectiveness: By using plastic materials that are less expensive and easier to work with, businesses can significantly reduce production costs. Rapid prototyping allows for smaller initial investments while still achieving high-quality results.
- Design Flexibility: The freedom to modify designs easily and quickly is one of the biggest advantages of rapid prototyping. Engineers can iterate designs based on feedback without the need for extensive tooling changes.
- Improved Communication: Physical prototypes facilitate better communication between design teams, stakeholders, and clients. They provide a concrete representation of concepts and allow for more effective discussion and decision-making.
- Testing and Validation: Having a physical prototype enables businesses to conduct real-world tests, leading to better validation of designs and ideas, ultimately reducing risks associated with full-scale production.
The Role of Rapid Prototyping in Metal Fabrication
The industry of metal fabrication relies heavily on precision and accuracy. Rapid prototyping plastic plays a significant role in this field, allowing engineers and manufacturers to produce metal components efficiently. Here’s how:
1. Design Verification
One of the foremost applications of rapid prototyping in metal fabrication is design verification. Before committing to metal, prototypes made from plastic can be used to ensure that the design meets specifications and functions as intended. This early stage verification helps prevent costly mistakes down the line.
2. Tooling and Fit Testing
When creating complex metal components, ensuring that each piece fits together perfectly is essential. Rapid prototyping allows manufacturers to create plastic parts for tooling and fit testing. Design flaws can be identified and rectified before the metal fabrication process, saving time and resources.
3. Low-Volume Production
Businesses often face the challenge of needing small volumes of specialized parts. Rapid prototyping plastic offers an ideal solution for low-volume production where traditional methods may be too costly or time-consuming. This approach allows businesses to meet specific client demands without overextending their budgets.
Technologies Used in Rapid Prototyping Plastic
Several technologies facilitate rapid prototyping with plastic materials. Understanding these methods is crucial for businesses looking to leverage this technique effectively:
- 3D Printing: Also known as additive manufacturing, this technology builds prototypes layer by layer from digital models. It is one of the most popular methods due to its speed and versatility.
- CNC Machining: Computer Numerical Control machining is used to cut and shape materials with high precision. It’s particularly useful for producing functional prototypes that require exact specifications.
- Injection Molding: This method involves injecting molten plastic into a mold to create the desired shape. It's effective for producing larger volumes of parts once the design is validated.
Choosing the Right Rapid Prototyping Plastic
Not all plastics are created equal when it comes to rapid prototyping. Different materials offer various advantages and are suitable for different applications. Here are some common plastics used in rapid prototyping:
- ABS (Acrylonitrile Butadiene Styrene): Widely used for its toughness and rigidity, ABS is ideal for prototypes that require durability.
- PLA (Polylactic Acid): A biodegradable plastic that is easy to print with, PLA is often used for prototypes that do not require extreme strength.
- Nylon: Known for its strength and flexibility, nylon is suitable for prototypes that will undergo stress and strain during testing.
- PETG (Polyethylene Terephthalate Glycol): This material provides a good balance between strength and ease of use, making it a popular choice for functional prototypes.
Future Trends in Rapid Prototyping Plastic
As technology continues to evolve, so too does the field of rapid prototyping plastic. Here are some trends that are shaping the future:
1. Advancements in Material Science
New materials are continually being developed, offering improved properties for prototyping plastic. Innovations in composites and specialty materials are expected to enhance the versatility and performance of prototypes.
2. Increased Automation
Automation in rapid prototyping processes streamlines production and reduces human error. As robotics and AI technologies advance, we can expect even greater efficiency and consistency in prototyping.
3. Sustainability Practices
With growing concerns about environmental impact, the industry is focusing on sustainable practices in rapid prototyping. This includes using recyclable materials and reducing waste during the prototyping process.
Conclusion
In summary, rapid prototyping plastic is an essential tool for businesses, especially in the highly specialized field of metal fabrication. Its ability to significantly enhance speed, cost-effectiveness, and flexibility cannot be understated. As advancements in technology continue to unfold, rapid prototyping will undoubtedly become even more critical for businesses striving to maintain a competitive edge in the evolving marketplace.
For companies like deepmould.net, understanding and utilizing rapid prototyping plastic technologies can lead to greater innovation, improved product development cycles, and ultimately, enhanced customer satisfaction. Embracing these practices is not just a strategy for success; it is a necessity in today’s fast-paced business environment.