Pumps in Hydraulics: Understanding Their Role and Importance
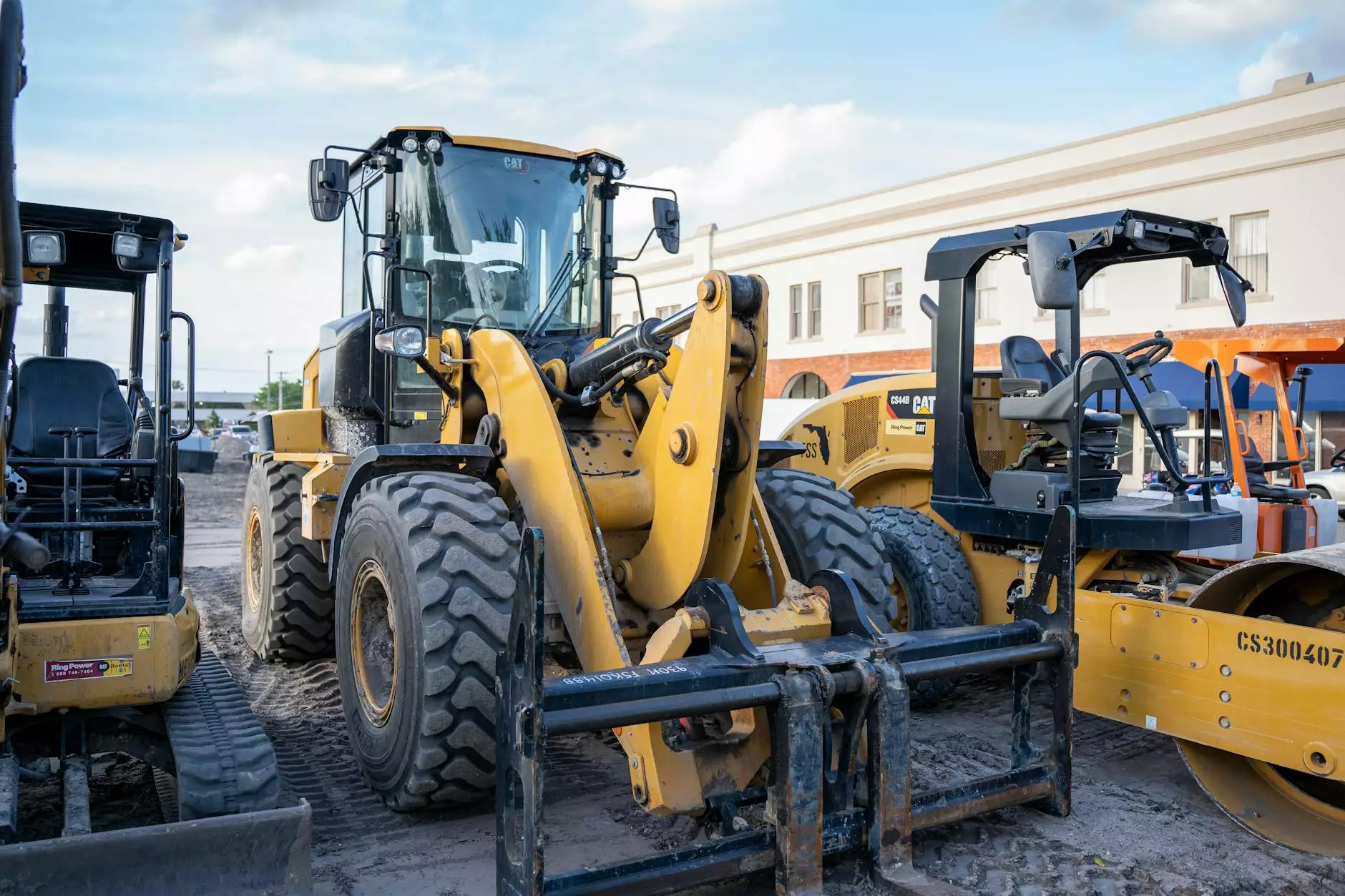
Pumps in hydraulics are pivotal components in the field of fluid mechanics, particularly in the automotive and motorcycle industries. Whether you are dealing with machinery, vehicles, or various systems that rely on hydraulic fluid to transmit power, understanding these pumps is essential. This comprehensive guide will delve deep into the nature of hydraulic pumps, their types, applications, and their significance in the automotive world.
What Are Hydraulic Pumps?
A hydraulic pump is a mechanical device that converts mechanical energy into hydraulic energy. It works by drawing hydraulic fluid from a reservoir and pressurizing it, which then allows for movement of machinery and systems. The functionality of these pumps is crucial in applications where controlled and precise movements are necessary.
Types of Hydraulic Pumps
There are several types of pumps in hydraulics, each designed for specific functionalities and applications. Below, we detail the most common types:
- Gear Pumps: These pumps use meshing gears to pump fluid by displacement. Gear pumps are known for their simplicity and reliability, making them widely used in hydraulic applications.
- Vane Pumps: These operate via rotating vanes that slide in and out of a housing. Vane pumps are favored for their smooth flow and quieter operations.
- Piston Pumps: Utilized in high-pressure applications, piston pumps use one or more reciprocating pistons to create pressure. They are highly efficient and capable of delivering a large volume of fluid.
- Screw Pumps: These pumps use a pair of screws to move fluid along the screw and are ideal for low-viscosity applications.
- Axial Piston Pumps: Common in construction and mobile hydraulic applications, these pumps provide efficiency at high pressures and variable flows.
How Hydraulic Pumps Work
The operation of hydraulic pumps can generally be divided into a few key steps:
- Fluid Intake: The pump draws hydraulic fluid from a reservoir through an inlet port.
- Pressurization: The mechanical action from the pump components compresses the fluid, building pressure.
- Fluid Discharge: The pressurized fluid is then expelled from the pump through an outlet port to perform work, such as moving hydraulic cylinders or motors.
Applications of Pumps in Hydraulics
Pumps in hydraulics are indispensable in many applications. Here are several critical areas where hydraulic pumps are prominently utilized:
1. Automotive Industry
In the automotive sector, hydraulic pumps play a role in various systems, including:
- Power Steering Systems: Hydraulic pumps assist in steering control, making it easier to maneuver vehicles.
- Braking Systems: Hydraulic pumps ensure efficient braking by applying pressure to brake pads.
- Transmission Systems: They help in the operation of automatic transmissions, providing fluid power to shift gears smoothly.
2. Motorcycle Parts and Supplies
In motorcycles, hydraulic pumps are essential for:
- Clutch Systems: Allowing smooth engagement and disengagement of the clutch.
- Brake Systems: Providing reliable stopping power through hydraulic brake systems.
3. Industrial Machinery
Hydraulic systems in industrial machines utilize hydraulic pumps for:
- Pressing and Forming: Performing heavy-duty work in manufacturing industries.
- Lifting and Rigging: Hydraulic systems dominate in construction and material handling.
Choosing the Right Hydraulic Pump
When selecting the right hydraulic pump, consider the following factors:
- Application Requirements: Understand the specific needs of your application, such as pressure and flow rates.
- Fluid Compatibility: Ensure the pump materials are compatible with the hydraulic fluid used.
- Size and Capacity: Choose a pump that fits the spatial and pressure requirements of your system.
- Efficiency: Select pumps that offer high efficiency to minimize energy consumption.
Maintenance of Hydraulic Pumps
To ensure a long lifecycle and reliable performance of hydraulic pumps, regular maintenance is imperative. Key maintenance tips include:
- Regular Fluid Checks: Monitor hydraulic fluid levels and quality, replacing fluids as necessary.
- Inspect for Leaks: Routine inspections help identify and remedy leaks before they escalate.
- Consider Filter Changes: Replace filters periodically to maintain fluid cleanliness and prevent contamination.
- Monitor Performance: Regularly observe performance parameters to detect any abnormalities.
The Future of Hydraulic Pumps in the Automotive Sector
The landscape of hydraulic technology is evolving, particularly in the automotive industry. Innovations are centering around:
- Electronic Control: The integration of electronic systems for precise control of hydraulic pumps.
- Increased Efficiency: Continued development of energy-efficient hydraulic systems helps reduce overall energy consumption.
- Environmentally Friendly Options: Increasing use of bio-based hydraulic fluids in line with sustainability trends.
Conclusion: The Importance of Quality Pumps in Hydraulics
In conclusion, pumps in hydraulics are fundamental to the operation and efficiency of various systems across the automotive and motorcycle sectors. Their ability to convert mechanical energy into powerful hydraulic energy makes them crucial for enhancing performance, safety, and reliability in vehicles and industrial applications. Companies like Shop Hydraulic America provide a vast selection of high-quality hydraulic pumps and parts, ensuring that automotive enthusiasts and professionals alike can find the right components for their needs.
By understanding the nuances of hydraulic pumps, their maintenance, and future trends, businesses can make informed decisions that bolster efficiency and reliability. This knowledge is invaluable in maximizing performance and maintaining operational efficiency across diverse applications.
For a comprehensive range of hydraulic pumps and expert guidance, visit Shop Hydraulic America today!