Plastics Injection Molding: A Comprehensive Guide to Business Success
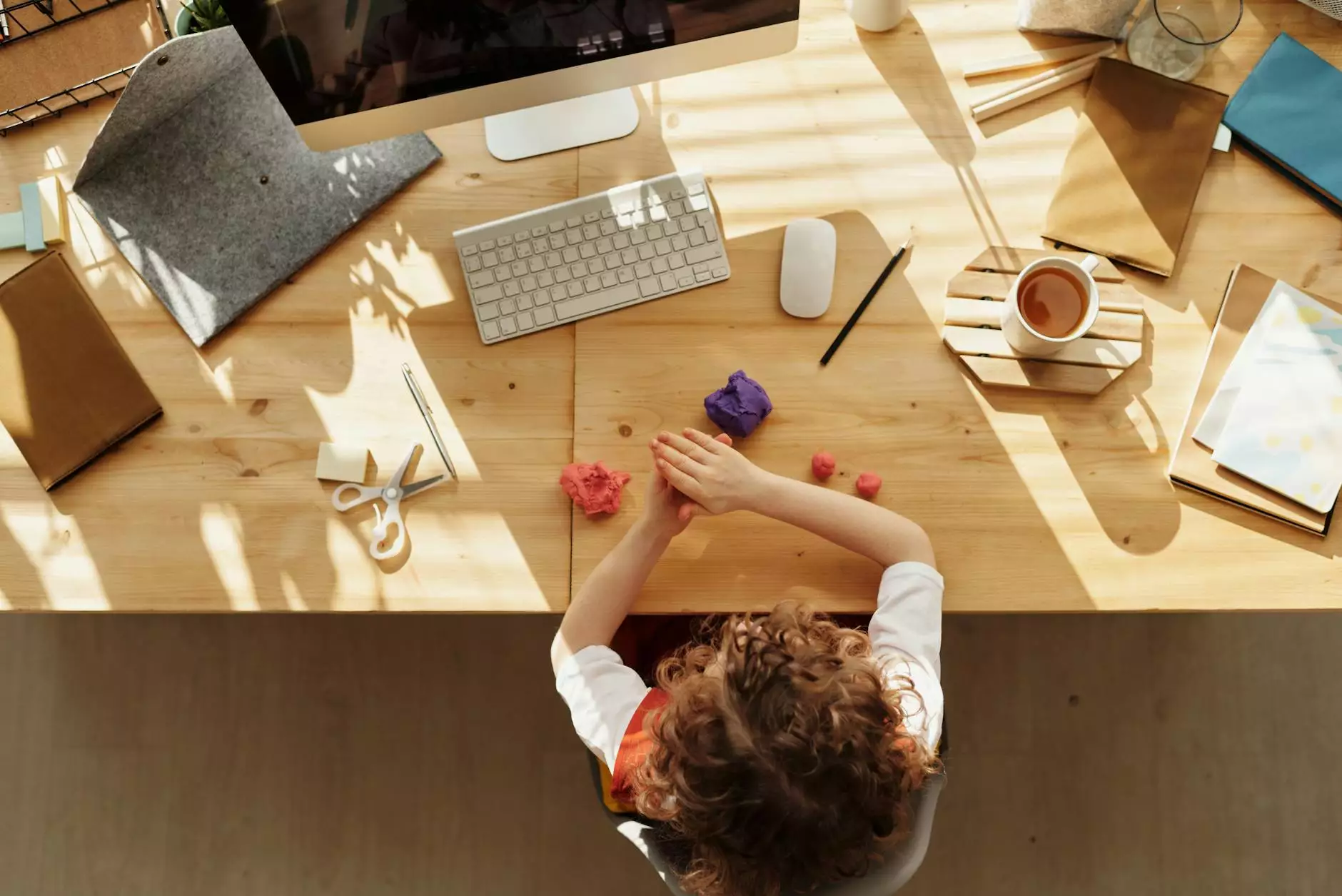
Introduction to Plastics Injection Molding
Plastics injection molding is undeniably a cornerstone of modern manufacturing processes. This incredible technology has revolutionized how businesses produce intricate plastic parts and components, providing unmatched efficiency, customization, and scalability. At the heart of this transformative process lies the ability to create detailed shapes and designs that cater to diverse industrial needs.
Understanding the Basics of Plastics Injection Molding
The Process Explained
The process of plastics injection molding involves several step-by-step actions that result in the formation of high-quality plastic products. Here’s a breakdown of the typical stages involved:
- Material Selection: The process begins with selecting the appropriate plastic material, based on the desired properties of the final product, such as strength, flexibility, and heat resistance.
- Melting and Injection: The chosen plastic resin is heated until it reaches a molten state. This molten plastic is then injected into a pre-designed mold under high pressure.
- Cooling: Once the mold is filled, the plastic cools and solidifies, taking on the shape of the mold.
- Mold Opening: After cooling, the mold is opened and the finished part is ejected.
- Finishing Processes: This final stage may include trimming, polishing, or assembling components to achieve the desired product quality.
Key Advantages of Plastics Injection Molding
Businesses leveraging plastics injection molding can enjoy a plethora of advantages that enhance productivity and profitability. Here are some of the primary benefits:
- High Production Rates: This process allows for rapid production of large volumes, making it ideal for mass manufacturing.
- Cost-Effectiveness: Although initial setup costs can be high, the long-term savings from scale production significantly reduce per-unit costs.
- Design Flexibility: With advanced technology, designers can create complex geometries and variations, catering specifically to customer needs.
- Minimization of Waste: The efficiency of this process reduces excess material use, promoting a more sustainable manufacturing approach.
- Feature-Rich Developments: Incorporating features such as ribs, textures, and bosses directly into the mold design can enhance functionality without additional manufacturing steps.
Applications of Plastics Injection Molding
The range of applications for plastics injection molding is extensive and touches various industries. Here are a few key sectors where this technology plays a pivotal role:
Aerospace and Automotive Industry
In the aerospace and automotive industries, lightweight yet durable plastic components are critical for enhancing fuel efficiency and performance. The ability to produce complex parts reliably makes injection molding a preferred choice.
Consumer Goods
The consumer goods sector consistently relies on plastics injection molding for producing items like household appliances, packaging, and electronic devices. The versatility in design allows manufacturers to innovate continuously.
Medical Devices
Healthcare-related products, especially medical devices, require stringent quality controls and precise specifications. Injection molding caters to this need, providing sterile and high-quality components for devices used in diagnosis and treatment.
Electronics
The electronics industry benefits from plastics injection molding through the production of lightweight and durable casings, connectors, and various components essential for device functionality.
Choosing the Right Partner for Plastics Injection Molding
When pursuing solutions in plastics injection molding, selecting the right manufacturing partner is paramount. For businesses seeking reliable services, DeepMould.net stands out as a leader in the metal fabricators category. Here are a few criteria to consider when choosing a partner:
Experience and Expertise
Look for a company with extensive experience in plastics injection molding. A seasoned provider can address complex challenges and optimize processes for superior outcomes.
Technology and Equipment
Advanced machinery and technology can significantly enhance production capabilities. Ensure that the partner utilizes state-of-the-art equipment that aligns with contemporary industry standards.
Quality Assurance Processes
Quality is non-negotiable in manufacturing. Choosing a partner who implements stringent quality assurance measures guarantees product integrity and reliability.
Customer Support and Communication
Effective communication is crucial in maintaining strong partnerships. Opt for a provider known for exceptional customer service to facilitate smooth operations.
Future Trends in Plastics Injection Molding
The landscape of plastics injection molding is continuously evolving. The following trends are shaping the industry:
Sustainable Practices
With an increasing emphasis on sustainability, manufacturers are exploring biodegradable and recyclable materials in injection molding processes. This not only reduces waste but also appeals to environmentally conscious consumers.
3D Printing Integration
The rise of 3D printing technology is paving the way for hybrid manufacturing processes that allow for increased customization and rapid prototyping, ultimately enhancing the overall efficiency of injection molding.
Smart Manufacturing
The incorporation of IoT (Internet of Things) and AI (Artificial Intelligence) in manufacturing environments enables predictive maintenance and process optimization, leading to significant cost savings and increased productivity.
Conclusion
In conclusion, plastics injection molding represents a vital aspect of modern manufacturing that offers unmatched benefits across various industries. By understanding its processes, advantages, and applications, businesses can harness this technology for enhanced operational efficiency and superior product quality. As we move towards a more sustainable and technology-driven future, companies like DeepMould.net are poised to lead the way, offering innovations in the metal fabricators space. Investing in the right plastics injection molding solutions is sure to pave the way for business success in today’s competitive environment.